Development and Characterization of Biological-based Construction Systems for Extraterrestrial Applications
Project Overview
(Click to expand)
I assisted in a summer Research Project funded by NASA Ames in Palo Alto, California as an Undergraduate Researcher over the summer of 2016. I worked with two graduate students on their thesis project working with a protein-bound composite created for the purpose of in-situ construction in extraterrestrial environments. The biopolymer solidifies regolith to form brick-like material, similar to concrete. This composite has been proposed as an extraterrestrial building material for in-situ construction, to reduce mission reliance on materials and structures that would otherwise be fabricated on earth My role in this project was to perform preliminary image analysis and mechanical and shrinkage testing of the Regolith Biocomposite (RBC). I have showcased my work both in the Stanford CEE VPUE conference and at the Stanford Opportunity Job Fair Reception on campus. The official write up for my portion can be found here:
​
Project Details
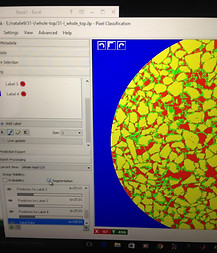

For this project, I began by conducting image analysis of micro-CT scans of the cross sections of the constructed RBC samples. I worked with a machine-learning program in ilastik to teach it to identify and segment the pore, soil, and protein regions of the scans, and applied it to over 8,000 similar images. I then compared the output data to the ratios recorded for the actual samples to ensure accuracy, and removed any outliers in the data.
I then performed autogenous and evaporative shrinkage measurements during sample molding, to determine the shrinkage coefficient of RBC. We manufactured groups of 5 RBC cylinder samples using 5 mixtures, and the samples were weighed and photographed both immediately after manufacture and after they had completely dried. We then compared the average diameters and heights for each sample at the two times to calculate shrinkage strain.

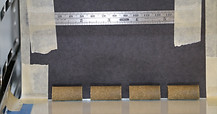
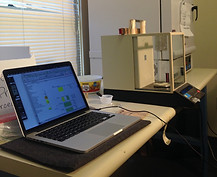
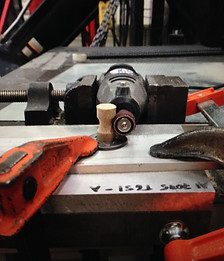



I then proceeded to conduct compression testing of RBC samples for sand, lunar soil simulant, and Mars soil simulant. We constructed cylindrical samples and sanded them down to hourglass shapes to encourage them to break in the center. The samples were secured to the uniaxial mechanical testing system with an adhesive, and subjected to axial tension forces until they cracked. As the composite material failed, a graph of the force vs displacement was recorded.
​
My projects proved successful for the summer:
ilastik was able to identify all three major
components of the micro-CT images with acceptable error; shrinkage testing showed a shrinkage strain between 0.6% and 1.6% (diameter); and uniaxial tensile testing showed tensile strengths close to that of concrete, the target material.